Észak-kelet Olaszország a cipészet Mekkája, a csizma és cipő gyártók szilícium-völgye. Ha lábfejre húzandó és olasz gyártmány, legyen az balettcipő vagy görkorcsolya, akkor az szinte biztos, hogy "az olasz csizma" szárának tetejéről származik: akárcsak a legnagyobb konkurensek az Alpinestarstól a Sidiig, a TCX üzeme is az ország iparilag legfejlettebb, Velence-székhelyű Veneto régiójában található, azon belül is a festői környezetben fekvő Montebelluna városában.
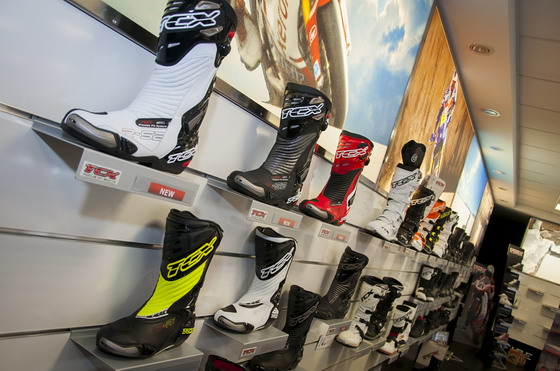
A TCX 1999-ben alakult meg azzal a céllal, hogy a motorkerékpározás szerelmesei számára kiváló minőségű, kényelmes és biztonságos lábbeliket kínáljanak, de mai nevükön csak 2008 óta ismerjük őket. Az eredetileg Oxtar néven bejegyzett céget ugyanis az után, hogy 2000-ben bemutatták az azóta is a márka high-end termékeit meghatározó, a komoly bokasérülések megelőzése érdekében kifejlesztett T.C.S. (Torsion Control System) rendszerüket és többek között ennek is köszönhetően néhány év alatt a motoroscsizma-gyártók élvonalába küzdötték fel magukat úgy a termékek minősége, mint az eladott darabszám tekintetében, egyik legnagyobb és legbefolyásosabb konkurensük, az Alpinestars beperelte őket nevük miatt - a kiejtett márkanévben a „star”, illetve az Oxtar logó csillaga zavarta őket, melyek miatt, szerintük, a vevők esetleg összetéveszthették a két márkát.
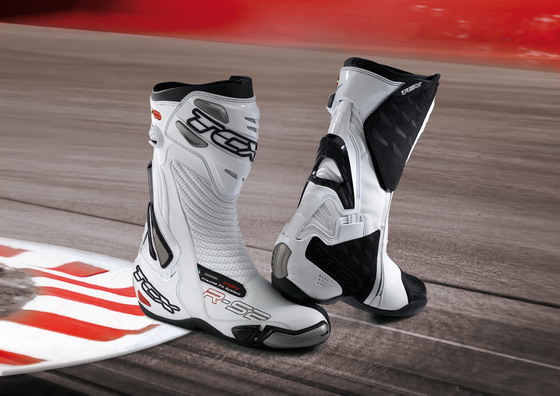
Az olasz bíróság a felperes javára döntött, a TCX-nek pedig nem maradt más választása: a magyarok által leginkább Talmácsi Gábor MotoGP-s lábáról ismert Oxtar csizmákat 2007 után TCX márkanév alatt fejlesztették és terjesztették tovább. A kulisszák mögött időközben, 2006-ban a cég irányítását átvette az olasz Novation Group, ez pedig nem csak szerkezeti és financiális megerősödést hozott a TCX számára, de mivel a cégcsoporthoz olyan neves és technikailag fejlett márkák is tartoznak, mint a Kayland (túra és hegymászó bakancsok), a Jolly (tűzoltó és munkabakancsok) és a Cosmas (lábbelik speciális alakulatok és fegyveres erők számára), a Novationön belül felhalmozódott elméleti, anyagismereti és kompozitgyártási tudásból a TCX azóta is rendületlenül profitál.
A TCX csizmák magyar importőre, az EuroMotor jóvoltából személyesen győződhettünk meg arról, hogy a laikus elképzeléssel szöges ellentétben milyen összetett, idő, alapanyag és munkaigényes, illetve a szakképzett személyzet számára fizikailag is mennyire megterhelő folyamat egy pár TCX motoros csizma legyártása. Ott jártunkkor éppen a MotoGP-ben és a Superbike világbajnokságon TCX-szponzorált versenyzők R-S2 típusú csizmái készültek.
Építsünk csizmát!
Egy pár TCX lábbeli létrejöttében a legelső lépcső a termék számítógépes megtervezése, kezdve a technikai jellemzőktől egészen a külső megjelenésig, ezt a feladatot a TCX házon kívül végzi. A csizmák tervezésében a TCX szakembereit specializálódott külsős dizájner cégek munkatársai segítik. Három-négy különböző, de szintén a régióban található olasz tervezőirodát foglalkoztat a TCX attól függően, hogy milyen termékükhöz milyen jellegű az éppen aktuális tervezési feladat. Miután a tervek elkészültek, jöhet az első prototípus legyártása.
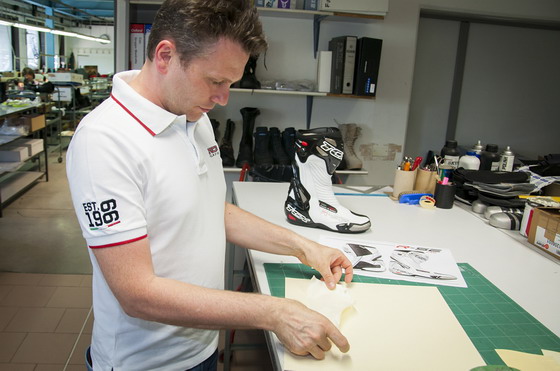
Kérdezzük meg bármelyik gyártót: ahhoz, hogy egy lábbeli kényelmes legyen, az egyik legfontosabb hozzávaló a kaptafa. Ez az a filléres költségű, csúnya és unalmas kinézetű, lábfej formájú fadarab, ami köré minden egyes csizma felépül. Ha a kaptafa lábanatómiai szempontból nem tökéletes formájú, akkor a csizma nem lesz kényelmes.
A kinyomtatott tervek alapján első lépcsőként háromdimenziós formát adnak a kétdimenziós rajznak. A kaptafára ragasztott, körberajzolt, majd lehúzott öntapadós lapok segítségével megkapják a csizma egyes alkotórészeinek szabásmintáját. Ezeket CAD programok segítségével bedigitalizálják, és már indíthatják is a 65.000 eurós, olasz gyártmányú, késes bőrvágó gépet, ami a perforált munkaasztalon átszívott levegővel simára feszített anyagból kivágja a csizma idomait.
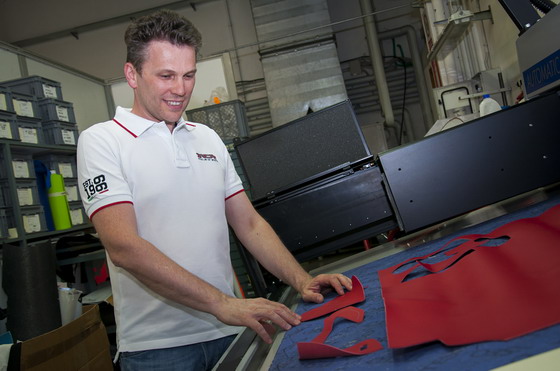
A sors fintora, hogy manapság ez a gép már csak elvétve vág igazi bőrt. A minőségi szintetikus műbőrök, gyűjtőnevükön microfiberek megjelenése óta sok konkurenséhez hasonlóan már a TCX is szinte kizárólag ilyen anyagból gyártja a csizmákat, kivételt képez néhány Gore-Tex membrános túracsizma. A legismertebb microfiber a Lorica nevű anyag, ami szinte minden jellemzőjében erősebb a borjúbőrnél, ráadásul tisztítása és karbantartása sem igényel akkora odafigyelést.
A szabásminta alapján kivágott idomokat és a Novation Group egyéb, a TCX-től legfeljebb tíz kilométeres távolságban lévő kompozitgyártó üzemeiből származó poliuretán alkatrészeket (mint pl. sípcsontvédő, boka és sarokrész, vagy maga a T.C.S. rendszer) ezután megkapják a varrónők, és megkezdődhet az érdemi gyártás. Az egytűs, speciálisan lábbeli gyártásra tervezett, német Pfaff varrógépeket magasan szakképzett helyi varrónők működtetik, akik a tervezési és gyártási részlegnél fontos beosztásban lévő szakemberekhez hasonlóan szintén a régióban található, cipészmesterséget tanító Centro Veneto Calzaturierón végeztek Stra-Venicében. Legtöbbjük már több mint tíz éve a cégnél van, és valószínűleg marad is, amíg munkaképes - professzionális szaktudás nélkül ebben az iparban nem terem babér, ezért a varrónőket roppant nagy becsben tartják cégen belül.

Miután a kaptafán a szorgos kezek alatt szimpla, dupla, vagy sokszor tripla varrás alkalmazásával összeállt a csizma feje és szára, a még alul-felül nyitott, félkész termékeket átszállítják a gyár egy némileg koszosabb, zsúfoltabb és csípősebb szagú részére, ahol először a belső, majd a külső talpat erősítik fel a csizmára különböző gépek és különleges anyagok felhasználásával. A folyamat természetesen sokkal összetettebb és bonyolultabb annál, mint amilyennek hangzik.
A csarnok legnagyobb és legfélelmetesebb gépe a belső talprészt házasítja a csizma fejével: egyszerre melegíti, nyújtja, préseli és varrja egymáshoz az antibakteriális és rezgéselnyelő réteget is tartalmazó, többrétegű belső talpat a microfiber és poliuretán felső részhez. A gyártás kulcsfontosságú része ez, hiszen ha itt vétenek hibát, akkor az adott termék azonnal selejtbe kerül, nem lehet kijavítani. A préselő-nyújtó-melegítő-varró apparátust természetesen szintén magasan képzett személyzet működteti, és mivel például a sarokrésznél és a lábujjaknál a „bőrt” különösen nehéz a megfelelő formára húzni, a gép meglehetősen nagy erőhatással dolgozik, nagy a sérülésveszély. A csizma itt már majdnem teljesen elkészült formát ölt, már csak a talp és egyéb apróságok hiányoznak róla.
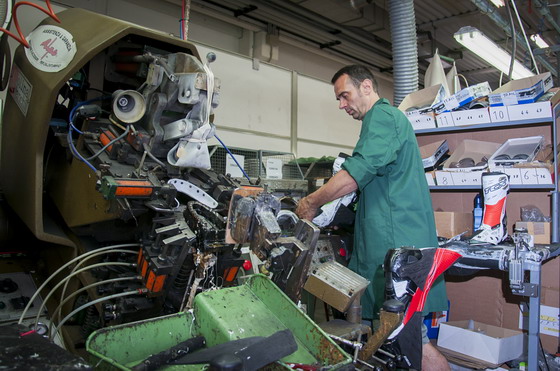
A külső talp felragasztása egy hatlépéses folyamat. Először egy nagy csiszolókoronggal megmunkálják a belső talp külső felét, hogy megkapják a ragasztáshoz szükséges felületet és eltávolítsák a nyújtás és varrás után maradó felesleges anyagot. Ezután ideiglenesen felhelyezik a talpat, és egy speciális tintát tartalmazó tollal körberajzolják. A külső talp körvonalai mentén ragasztószalagal körbemaszkolják a csizma alját, nehogy a rendkívül agresszív és erős ipari ragasztó kárt tegyen a csizma nem ragasztandó részeiben, majd felkenik a ragasztót a talpra.
Maga a konkrét ragasztás három fázisból áll. Először előmelegítik a csizma talpát, hogy a magas poliuretán tartalmú ragasztóanyag aktiválódjon, majd gyorsan a helyére illesztik a külső talpat, és a terméket egy csizmaformájú présgépbe helyezik. Az itt eltöltött fél perc során a csizma talpa szinte összeolvad a belső talppal és a műanyag-microfiber kombinációjából álló szárral (egyes termékek, mint például a sokkal összetettebb talpkonstrukcióval készülő krossz csizmák kétszeres présgép-kezelést kapnak), majd, hogy a ragasztás folyamata gyorsan lezáruljon, minden csizmát végigküldenek egy -20 Celsius fokon működő, futószalagos mélyhűtőn. A körülbelül 700 ezer euró értékű, kizárólag olasz gyártmányú gépeket tömörítő gyártósoron ez az utolsó nagyobb gép.
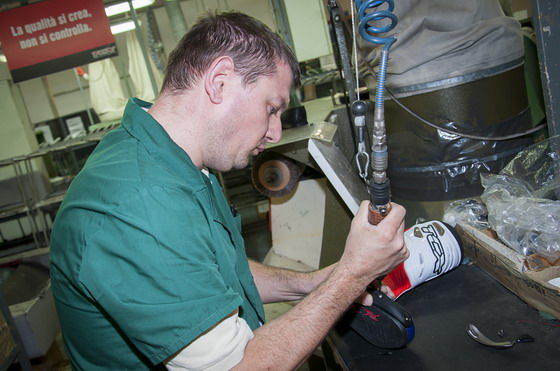
Az R-S2 esetében végül még felcsavarozzák az orrkoptatót és a lábfej első része és a lábujjak sérülése ellen kifejlesztett, a T.C.S.-hez hasonlóan szintén TCX-szabadalom M.C.S. rendszert, és ezzel el is készült egy újabb pár TCX R-S2 sportcsizma. De mielőtt még a viszonteladói hálózat felmarkolná a csomagolt terméket majd a világ valamelyik pontján egy motoros lábán kötne ki, még hátra van a gyártási ciklusonként szúrópróba szerű minőségellenőrzés. Mivel a TCX a Gore-Tex-szel is együttműködik, a minőségellenőrzési labor is jobban felszerelt az átlagnál: mulatságos volt azt nézni, amint az ellenőr munkatárs locsolókannából önti tele vízzel a Gore-Texes túracsizmát, hogy aztán a Gore saját gépén végzett centrifugás vizsgálat kiderítse, valóban százszázalékos-e a vízállóság.
Az egyetlen, nem is olyan apró szépséghiba mindebben azonban az, hogy az általunk Montebellunában meglátogatott TCX gyártósor az ürességtől kongott. Alig egy maroknyi ember jött-ment az üres polcok és pihenő gépek között, érzésre ők is leginkább a mi gyárlátogatásunknak asszisztáltak, mint tényleges gyártást végeztek. Az oka ennek egyáltalán nem egyedi: 2012-től a teljes TCX gyártás átkerült a cég romániai és kínai partnereihez, Olaszországban már csak az egyedi megrendelésű termékeket készítik, mint például a szponzorált versenyzők csizmáit. Ugyanakkor a minőségellenőrzés, az alapanyagok egy része, illetve a komplett gyártósor is mind olasz, tehát a munkásbéreken való spórolás elvileg nem mehet a minőség rovására.
A TCX volt az első olyan gyártó, akinek minden terméke megkapta a CE minősítést, beleértve az utcai jellegű Urban sorozat motoros cipőit is
És hogy nem is megy, annak a TCX partnerei a legjobb bizonyítékai. Az évek során a TCX és anyacége, a különböző autóipari karbon alkatrészek gyártásában is nagy elismerésnek örvendő Novation Group szaktudását felfedezte magának számos olyan gyártó, akiknek azóta bérgyártásban készíti a lábbeliket a TCX.
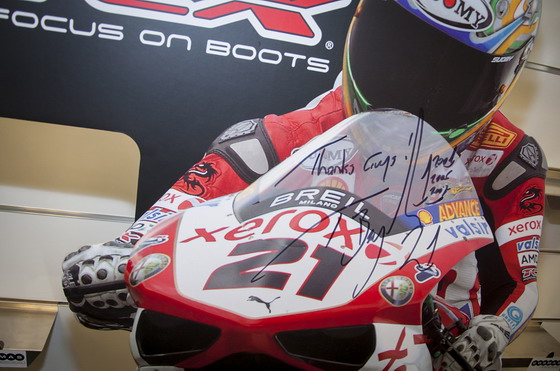
A teljesség igénye nélkül talán elég annyi, ha eláruljuk, hogy a BMW Motorrad, a Polo és a Hein Gericke motoros csizmáit már évek óta a TCX gyártja, de újabban már a Ducati számára is szállítanak bolognainak brandingelt, de hatalmas elismerésként a TCX logót továbbra is magukon hordó sportcsizmákat. Sőt, az amerikai motokrossz két legnagyobb sztárja, Ryan Dungey és James Stewart lábán feszülő Nike AIR MX 6.0 névre hallgató, kereskedelmi forgalomban nem kapható krosszcsizmákat is a TCX gyártja az amerikai sportszeróriás számára. Ennyit a TCX minőségről...